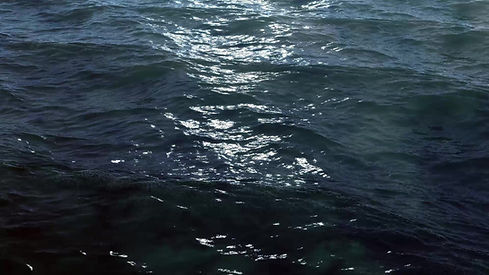
Project Structure
Workplan
The total duration of REFOS project is 42 months (July 01, 2016 – December 31, 2019). The work programme aims at properly coupling the dynamic behaviour of the individual components of the complex structure (W/T, OWC, floater, moorings, etc) into an integrated computational tool describing the dynamics of the whole system. Furthermore, a whole-life cycle approach will be used to optimize the structural design, mainly in terms of fatigue design of critical structural components. The project work plan is made up of theoretical, experimental and administrative tasks, grouped in nine (9) work-packages, described below:
PHASE I: Environmental Parameters, Lay-Out, Sizing and Global Analysis of the Multi-Purpose Floating Structure with its Components
Work package 1: Basic design parameters and environmental conditions: To define the design workspace of the system and perform preliminary sizing (gathering of environmental data; defining the environmental design conditions for the selected locations having a water depth of 200m approximately; establishing the general layout and sizing of the floating structure and its components (OWC device, W/T), the operating conditions and specification of the W/T (diameter, rated power, structural characteristics of the tower, the aerodynamic characteristics of the blade profiles, maximum allowable deflections, limiting acceleration values, etc.); performing hydrostatic calculations; determining the loading cases; evaluating the aerodynamic and aero-elastic loads on the wind turbine (W/T).
Work package 2: Coupled hydro-aero-elastic analysis for the determination: To analyse the coupled behaviour of the moored multi – purpose floating system and conclude the design of its components in full scale. The WP includes: (a) evaluation of the frequency-dependent first- and second-order hydrodynamic characteristics of the floating structure with the OWC, (b) evaluation of the dynamic pressure fluctuation and the associated air flow rate for the dimensioning of the OWC’s air turbine, (c) mooring / tendons system analysis and design, (d) coupled hydro-aero-elastic analysis of the moored floating multi-use platform by solving the equations of motion in the frequency and the time domain, (e) evaluation of shear forces and moments at the mooring – structure connections, at the floater – brackets joints and at the tower – floater connections.
Work package 3: Air turbine design for wave energy production: (a) To define the geometry, the aerodynamic sizing and the operating characteristics (tip diameter, height, cord and number of blades, clearances, rotational speed, dump coefficient, torque etc.) of a Wells type air turbine with variable pitch based on the wave potential characteristics of the locations studied in WP1 as well as on the hydrodynamically optimized pressure head and the reciprocating air volume rates inside the OWC chamber , obtained in WP2. The air – turbine optimization will be carried out using the methodology described in [R20] (b) to design an equivalent small scale air-turbine and experimentally investigate its operating characteristics in order to be used in the water tank scaled tests (WP6).
PHASE II: Design and Analysis of Steel Components, Structural and Hydrodynamic Testing
Work package 4: Structural analysis and design of steel tower, the floating supporting structure and selected components: (a) To account for the structural design of the steel tower with particular attention at the connection between tower and the floating supporting structure (ultimate strength and fatigue); (b) To account for the structural design of steel floating supporting structure with emphasis on the design of braces (ultimate strength), of tubular connections (ultimate strength and fatigue), and on the design of special details; (c) To perform the design the TLP tendons.
Work package 5: Testing of key steel components and numerical simulations: (a) to design and conduct tests of key steel components under cyclic loading (floater – brackets joints, tower – floater connections, tethers); (b) to manufacture the required components to be tested; (c) to carry out stress analysis of the tested structural components using finite elements techniques; (d) to conduct a parametrical study of critical components to improve their fatigue life.
Work package 6: Wave tank experimental campaign and analysis of measurements: (a) To design and conduct physical model tests in the wave tank of the Laboratory of Ship and Marine Hydrodynamics, NTUA, with a scaled- down model of the REFOS energy platform equipped with a scaled 10MW W/T for operational and extreme environmental conditions at the selected sites; (b) to conduct experimental campaign with the existing 1/40 scaled – down model of a floating multi-purpose structure equipped with a 5MW W/T and the newly designed air-turbine in WP3 for sea state conditions at the selected REFOS installation locations. The inertia characteristics of the W/T and the scaled wind thrust on W/T the will be properly accounted for, together with the damping characteristics of the OWC’s device (see WP3) and the moorings; (c) to construct the integrated scaled – down model of the REFOS energy platform supporting a 10 MW W/T and OWC’s devices and conduct experiments; (d) to analyse the experimental data and validate numerical models by comparison with experimental results.
​
PHASE III: Final Design and Techno-economic Feasibility Analysis
Work package 7: Development of the REFOS final design: Based on the structural analysis, the experimental testing and numerical simulations of components, the final design of the investigated configuration will be conducted.
Work package 8: REFOS techno-economic feasibility analysis and dissemination of the results: (a) to collect techno – economic data dealing with the development of floating multi – purpose structures; (b) to detail the particular issues that will be raised during their deployment for the selected installation locations; (c) assessment of the operational cost, the maintenance cost for the selected installation locations; (d) to disseminate the project achievements in dedicated Workshops.
COORDINATION
Work package 9: Project Management & Coordination: To coordinate the project’s implementation and the collaboration between the members of the project’s scientific team; to stewardship the project’s scientific and budgetary progress according to schedule, to organize the program’s progress meetings, to write up and submit the yearly progress- and final-report.
